Selecting the right type of self-tapping screw can significantly impact the performance and longevity of your project. Self-tapping screws are designed to drill their own hole as they are driven into materials, making them incredibly useful for a variety of applications. However,
understanding the different types and their specific uses is crucial. This article delves into the diverse world of self-tapping screws, offering insights that ensure optimal use in varied applications.
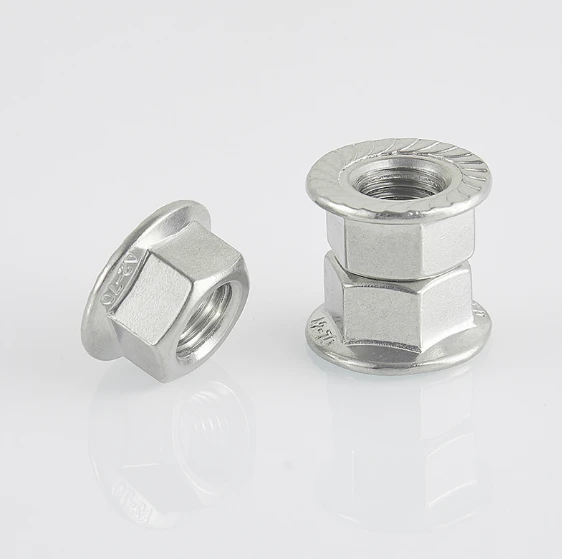
Pan Head Self-Tapping Screws are often used in applications where the screw head is not recessed. They feature a flat head with a rounded top, perfect for applications requiring a larger surface area under the head. The design provides superior holding power and is particularly favorable in electrical applications where space for screw heads is limited. This type of screw is commonly crafted from stainless steel or zinc-plated steel, providing robust resistance to corrosion, which is critical in environments that experience high levels of moisture.
Flat Head Self-Tapping Screws differ in that they are designed to sit flush with the material’s surface. Ideal for projects requiring a smooth finish, they are extensively used in cabinetry and woodworking. Their design ensures that they don't protrude above the surface, which is advantageous for aesthetic purposes and in applications where surface protrusion is undesirable. They are typically used in wood, but variations are available for metalwork.
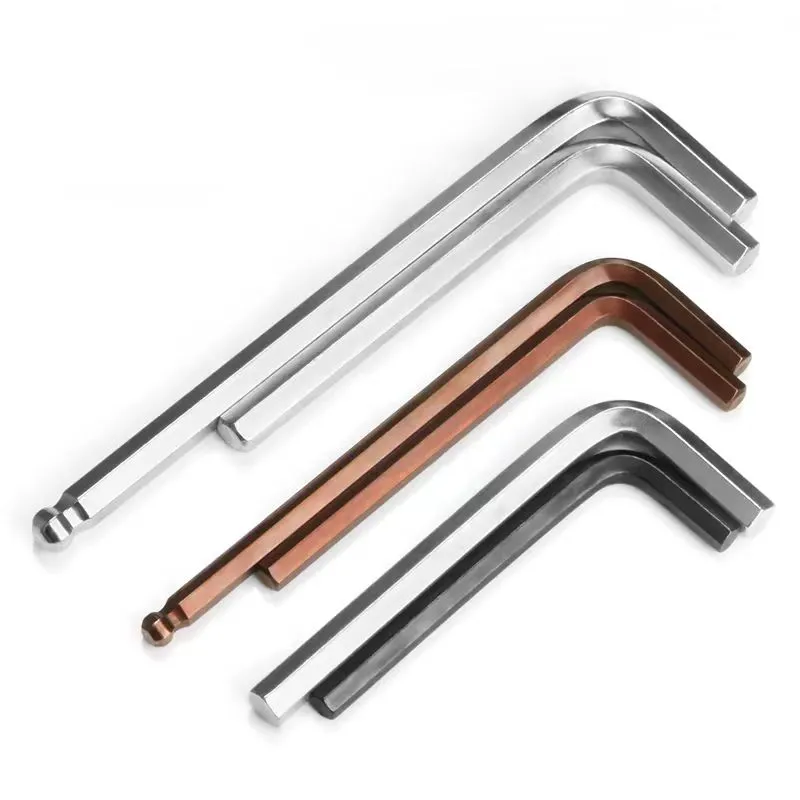
Hex Head Self-Tapping Screws are characterized by their hexagonal head, enabling the use of a wrench for increased torque. This feature is particularly useful in construction and assembly applications where precise torque application is essential. These screws are ideally used in metal-to-metal and heavy wood applications. Their construction allows them to handle significant stress and load without stripping the material or the screw itself.
Self-Drilling Screws are equipped with a drill-like flute, eliminating the need for a pilot hole. This not only saves time but also reduces the need for additional tools. These screws are ideally used in metal applications where a quick assembly is desirable. Their efficiency in drilling reduces labor costs significantly and minimizes the risk of material damage.
different types of self tapping screws
Countersunk Self-Tapping Screws provide a neat finish by allowing the head to sink into the surface. Used extensively in applications where a flawless finish is necessary, these screws eliminate the need for follow-up refinishing. Commonly used in joinery, furniture making, and where wood aesthetics are critical, these screws help maintain the natural beauty of the wood by ensuring a seamless surface.
Button Head Self-Tapping Screws are known for their aesthetic appeal and functional strength. The broader head offers a larger contact surface, which is beneficial in soft materials like plastic. The button head offers a dome-shaped profile that not only looks sleek but distributes load effectively, reducing the risk of material deformation.
Another vital category is the Winged Self-Tapping Screw, designed for use in drywall applications. The innovative wing design assists in creating a pathway through the drywall before the wings break off when they reach the wood or metal substrate, allowing the screw to tap into the subsequent layer securely. This design is invaluable in minimizing the damage to the surface layer, ensuring a secure and firm hold between layers.
When choosing self-tapping screws, material composition is just as important as the design itself. The two most common materials are stainless steel and carbon steel. Stainless steel screws are known for their resistance to corrosion and staining, while carbon steel screws provide enhanced strength and durability, making them ideal for heavy-duty applications. Understanding the environment and load requirements is crucial when selecting the appropriate material.
The correct deployment of self-tapping screws can drastically augment the integrity and longevity of assemblies in construction, automotive, and everyday household applications. Ensuring optimal compatibility between the screw type and the application material is paramount to achieving desired results. By selecting the right type of self-tapping screw, one can ensure not only the structural integrity of their project but also achieve efficiency, cost-effectiveness, and durability.