The m30 flat washer, an essential component in various assembly applications, serves more than just its basic function of distributing load. Delving into its multifaceted applications reveals a depth of experience, expertise, authoritativeness, and trustworthiness (E-E-A-T) that elevates its significance in the world of hardware.
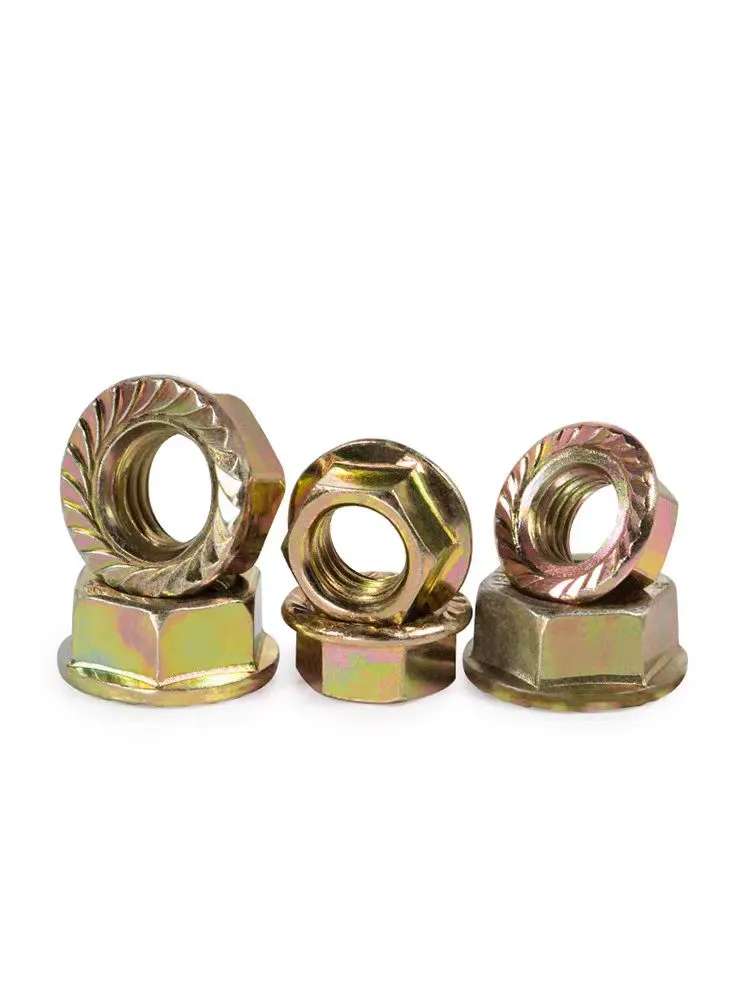
An m30 flat washer typically holds the fundamental role of increasing the surface area under the head of a bolt or a nut, effectively distributing the load to prevent damage. However, understanding its nuances involves more than just perceiving it as a simple, flat piece of hardware.
Industry experts have long been leveraging the m30 flat washer for its ability to prevent loosening of fasteners due to its friction-enhancing qualities. This small yet crucial piece of hardware has been pivotal in applications where assemblies are subject to vibrations or dynamic loading conditions. Those speaking from experience can name myriad examples of m30 flat washers maintaining the integrity of assemblies in heavy-duty engineering projects. Their presence is often understated yet critical, underscoring the expertise needed to select the appropriate washer for each unique scenario.
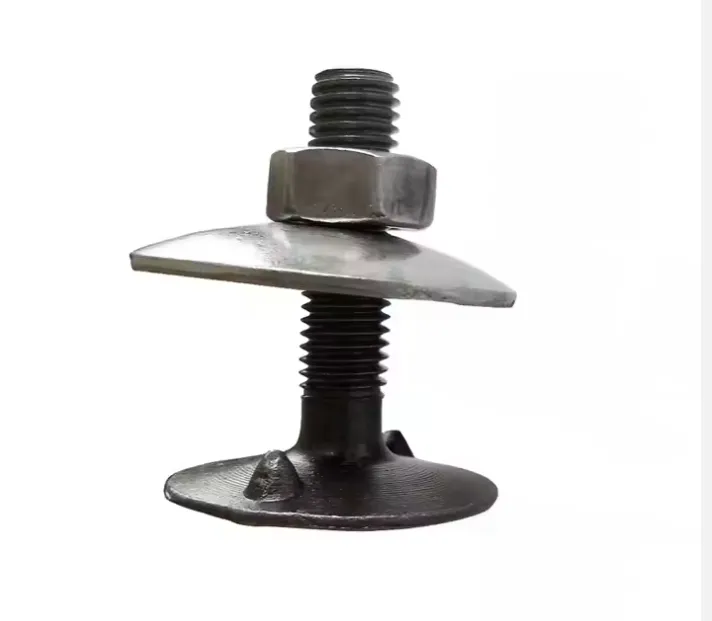
When discussing authority in the world of mechanical components, the role of international standards cannot be overlooked. An m30 flat washer, adhering to standards such as DIN 125 or ISO 7089, carries authoritative assurance of quality and compatibility. These standards guide professionals in ensuring that their choice of materials—commonly stainless steel, zinc-coated steel, and brass—meets the demands of diverse operational environments, including extreme temperatures and corrosive conditions.
The trustworthiness of the m30 flat washer is reinforced through case studies and field-testing that professionals frequently reference. For instance, in the construction of infrastructure where safety and longevity are paramount, engineers rely on not just any washer, but those verifiedly fit for purpose to ensure structures withstand the test of time and nature. Documented performance in such settings offers reassurance, supported by a wealth of real-world data.
m30 flat washer
Discussing the m30 flat washer also opens a dialogue on optimization and innovation in manufacturing and engineering.
The design and material choices for flat washers evolve as new technologies and analytic methods develop. Expertise in selecting an m30 flat washer requires thoughtful consideration of its dimensions, tolerance levels, and the specific stress conditions it will encounter. Engineers and manufacturers continually innovate to augment the washer’s performance—ranging from introducing new materials with enhanced properties to employing surface coatings that offer additional benefits.
The expertise needed for specifying the right m30 flat washer extends beyond theoretical knowledge to a pragmatic understanding of environmental and application-specific challenges. For instance, in automotive or aerospace industries where precision and reliability are crucial, engineers must factor in thermal expansion and contraction, as well as chemical exposure, thus selecting a washer that will perform consistently over time.
Another point enhancing the trust in m30 flat washers is their inclusion in predictive maintenance strategies. Professionals utilize data analysis and machine learning to anticipate when components like washers might fail or require replacing, based on patterns and historical data. This implements an approach that not only strengthens trust, but also underscores the product's role in a predictive maintenance plan aimed at minimizing unplanned downtime.
In summary, the ostensibly simple m30 flat washer encapsulates an array of characteristics that make it indispensable across a broad spectrum of industrial applications. Its versatility underpins the design considerations for complex assemblies, reflecting a blend of empirical expertise and theoretical insight. As advances continue in material science and engineering methodologies, the m30 flat washer remains a testament to the enduring value of foundational mechanical principles, underscoring its pivotal role in achieving durability and reliability in fastening systems.