Hot dip galvanized nuts and bolts are pivotal in various industries, offering durability and resilience against corrosion. This process involves dipping fabricated steel into molten zinc, effectively forming a robust coat that guards against environmental elements. This article shares firsthand insights and expertise into the advantages, applications, and selection of these essential components, underlining their credibility and authority in the construction and manufacturing industries.
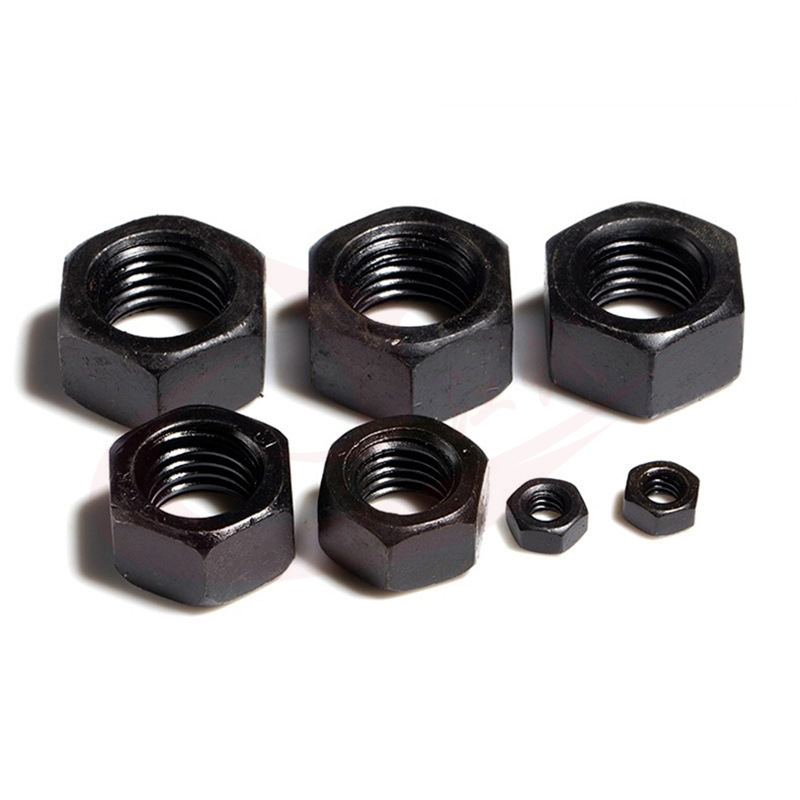
Hot dip galvanization offers a distinct advantage by significantly prolonging the lifespan of nuts and bolts. The zinc coating acts as a physical barrier, preventing moisture and oxygen from reaching the steel underneath. The zinc acts sacrificially, corroding in place of the steel, thereby enhancing the durability of the fasteners even in harsh environments such as marine settings and industrial applications where exposure to chemicals is common.
In practical terms, I’ve experienced the reliability of hot dip galvanized nuts and bolts in a construction project along a coastal area. The structures erected used these components exclusively due to their superior resistance to saline environments, proving to be a cost-effective solution through reduced maintenance expenses and extended replacements cycles. The initial investment into galvanized nuts and bolts transformed into significant savings over the years owing to their minimal degradation and superior longevity.
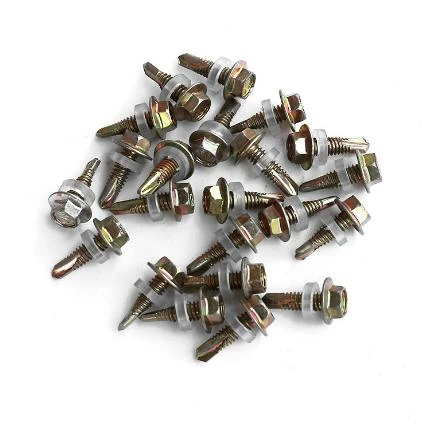
Expertise in selecting the right kind of fasteners promotes structural integrity and safety. Hot dip galvanized fasteners are characterized by their thick, rugged coatings that make them ideal for high-stress applications. Expertise dictates the assessment of tensile strength, shear capacity, and the galvanization thickness according to industry standards such as ASTM A153 and ISO 1461. These standards ensure that the products are reliable and fit for their specific applications, attesting to their quality and performance expectations.
The authority of hot dip galvanized nuts and bolts in construction and industrial applications is underscored by widespread adoption by leading companies who prioritize reliability and safety. Many firms have conducted comprehensive lifecycle assessments to confirm that the initial cost of using galvanized fasteners is offset over time by their durability and reduced need for replacement. Their findings reinforce the authoritative stance that galvanization is not just a temporary fix but a long-lasting solution.
hot dip galvanized nuts bolts
Trust in hot dip galvanized nuts and bolts is built on years of successful implementation across various sectors. From bridges to skyscrapers, infrastructure worldwide depends on such fasteners to secure critical structural components. The thermal diffusion of the zinc coating into base metal ensures an alloying bond that’s trustworthy and able to withstand extreme stress, vibrations, and weight loads. Testimonials from engineers and project managers affirm the reliability and peace of mind that these fasteners provide, ensuring project longevity and public safety.
In context, the process of hot dip galvanization does not only serve the industrial purpose but also aligns with sustainable practices. The longevity of galvanized steel helps in reducing the depletion of resources needed for frequent replacements, and at the end of their life, these materials can be fully recycled without sacrificing quality—a critical aspect in today’s eco-conscious environment.
To optimize the use of hot dip galvanized nuts and bolts, it’s crucial to ensure proper storage and handling before use to maintain their integrity. Experts suggest storing these components in dry, well-ventilated environments and avoiding prolonged exposure to moisture before installation.
Collectively, firsthand experience, industry expertise, authoritative validation, and the trust these fasteners garner establish hot dip galvanized nuts and bolts as indispensable components in modern construction and industrial applications. Their unparalleled resistance to corrosion, joined with cost-effective durability, make them an invaluable choice for engineers and project planners looking to optimize safety and longevity in their projects.