In the intricate world of manufacturing and construction, the selection of nuts and bolts is pivotal to the integrity and durability of any project. As an experienced engineer with two decades of hands-on experience, I've come across an astounding array of nuts and bolts, each with its own unique set of features and applications. This arsenal of fasteners is crucial to the assembly of everything from high-rise buildings to household furniture. Understanding these components ensures not only the success of a project but also safety and efficiency.
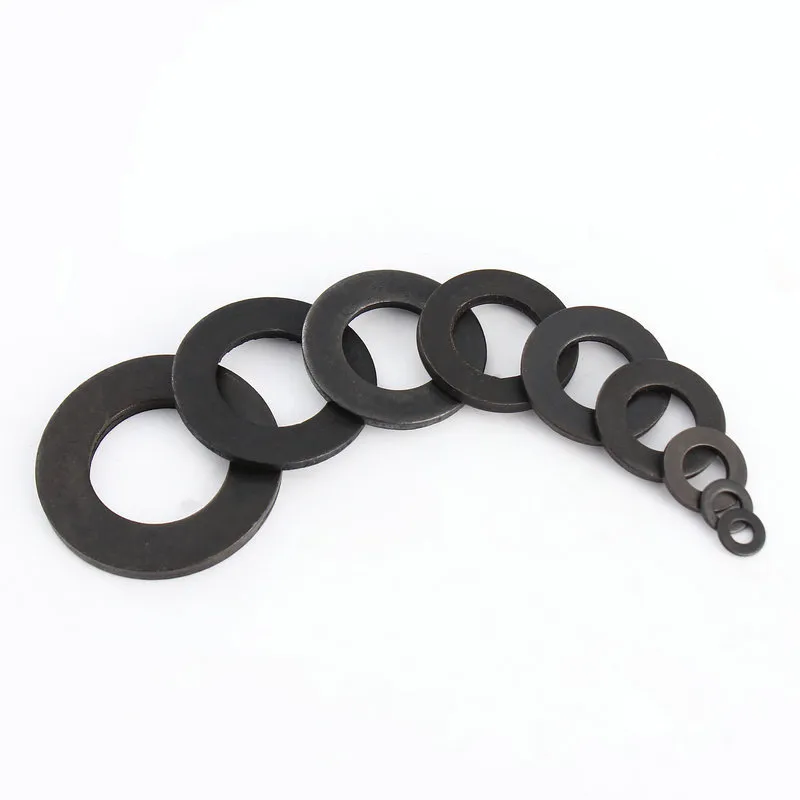
Nuts and bolts, while often used together, come in a variety of styles, each designed for specific applications. Bolts, the long, sturdy fasteners, are paired with nuts to secure components together. Among the most common types of bolts is the hex bolt, known for its six-sided head, making it easy to grip with a standard wrench. These bolts are often utilized in construction and engineering due to their simplicity and strength.
Another popular form of bolt is the carriage bolt, characterized by a domed head and a square neck. The square neck prevents the bolt from turning as a nut is tightened, making it ideal for woodworking where both appearance and functionality are important. Lag bolts, often referred to as lag screws, are used in wood construction for their strong thread that grips wood securely.
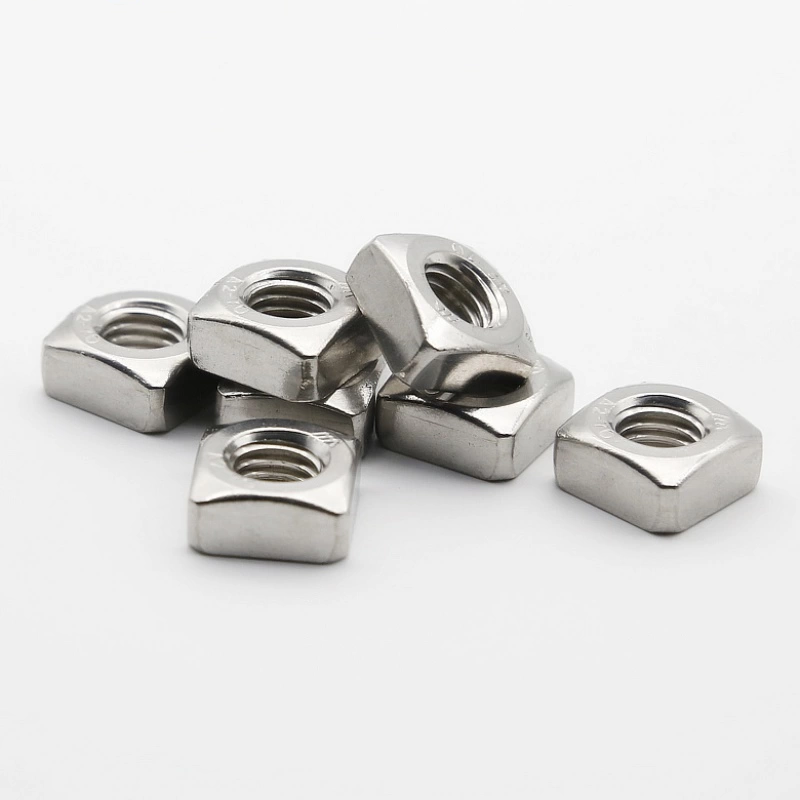
On the nut side of the pairing, hex nuts are the standard accompany to hex bolts and can be found in nearly every toolkit. For applications where vibration is a concern, lock nuts are preferred. These are equipped with nylon inserts or other mechanisms to prevent loosening under stress.
Flanged nuts, with a wide surface area, distribute pressure evenly, making them suitable for applications where load distribution is critical. Wing nuts offer easy hand-tightening and are particularly useful in applications requiring frequent disassembly.
Materials also play a crucial role in the selection of nuts and bolts. The most common material is steel, valued for its strength and durability. For areas exposed to moisture and elements, stainless steel or galvanized bolts provide added corrosion resistance. In high-temperature applications, bolts crafted from materials like titanium or high-grade alloys are imperative for maintaining structural integrity.
types of nuts and bolts
The manufacturing process of nuts and bolts also affects their suitability for different tasks. Precision-made fasteners, crafted with tight tolerances, ensure optimal fit and performance, which is critical in high-stakes environments like aerospace or automotive engineering.
Beyond understanding the types and materials, correct usage is critical. Improper installation can lead to bolt failure, which is often catastrophic. Achieving the correct torque—consistent with the bolt’s specification—ensures a secure, reliable joint. Over-tightening can be as detrimental as inadequate tightening, leading to stress fractures or thread stripping.
In the evolving landscape of manufacturing, the ongoing development of smarter materials and coatings continues to enhance the reliability and versatility of nuts and bolts. For instance, recent advances in polymer coatings are providing even greater resistance to corrosion and friction, extending the lifecycle of fasteners in challenging environments.
The ubiquitous presence of nuts and bolts across industries underlines their importance; yet, their selection and application demand careful consideration. By staying informed and adhering to industry standards, professionals can ensure their projects stand the test of time.
As someone deeply embedded in this field, I cannot overstate the importance of selecting the right type of nut and bolt for your specific needs. Understanding the nuance and technical specifications of these components not only brings efficiency and safety to projects but also fosters innovation and advancement. The foundation of your work—literally and figuratively—rests upon these small yet mighty components.