When it comes to creating robust and secure assemblies,
the M12 serrated washer stands out as a critical yet often overlooked component. As someone who has spent over a decade in the world of industrial fastening solutions, I can attest to its indispensable role in ensuring the reliability and longevity of bolted joints. It’s not just a piece of metal; it’s a guardian against the perils of loosening caused by vibration and dynamic loads.
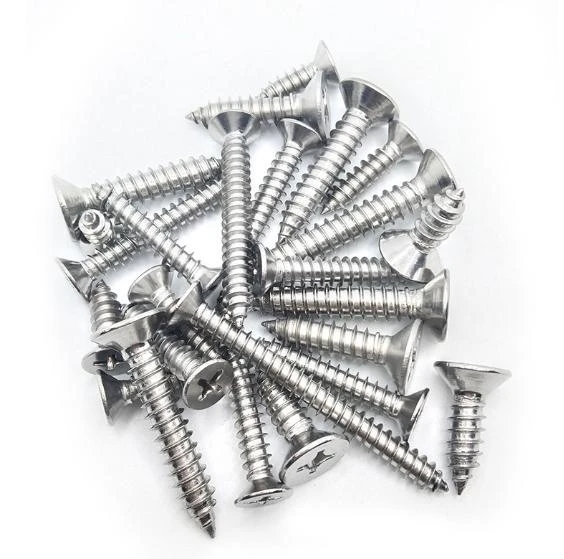
Why the M12 Serrated Washer is Essential
Experience has taught me that the failure of even a single bolt can lead to catastrophic outcomes, particularly in high-stress environments such as automotive engines, aerospace components, or heavy machinery. The M12 serrated washer, with its unique toothed design, provides extra grip to the nut and substrate, minimizing the risk of self-loosening. This mechanical locking feature enhances the friction between the surfaces, which is vital in maintaining the integrity of the assembly under variable load conditions.
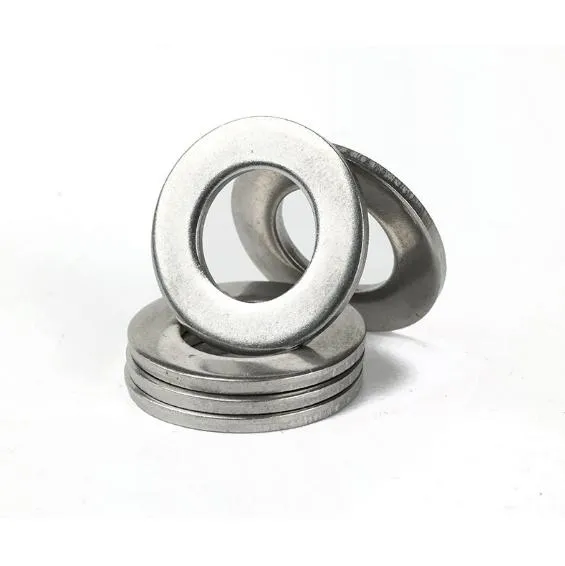
Professional Use Cases in High-Performance Sectors
In my years of professional experience, I have seen the M12 serrated washer repeatedly prove its worth in various high-performance sectors. Automotive engineers, for example, rely on these washers in engine mounts, where intense vibrations are common. The aerospace industry, with its stringent safety and reliability standards, often employs serrated washers in critical joints to mitigate the risk of joint failure during flight. These washers also find utility in the manufacturing of wind turbines, where they ensure the structural stability required to withstand incessant environmental forces.
Manufacturing Expertise and Quality Assurance
m12 serrated washer
Manufacturers of the M12 serrated washer understand the necessity of precision engineering and quality assurance. Top manufacturers invest in state-of-the-art technology and rigorous testing protocols to produce washers that exhibit consistent performance under stress. The attention to material selection, typically involving high-strength alloys or corrosion-resistant stainless steel, ensures durability and performance. As a professional in the field, I insist on sourcing washers from reputable companies that adhere to the highest quality standards, such as ISO certifications, to guarantee reliability.
The Authority of Engineering Standards
The M12 serrated washer's reliability is backed by recognized engineering standards and practices. Compliance with standards such as DIN 6798 (the German standard for serrated washers) or the ANSI/ASME guidelines in the U.S. is a testament to its authority in the engineering community. These standards specify the dimensions, material properties, and performance tests that guarantee a washer's capability to perform as expected in demanding applications.
Trustworthiness by Field-Tested Validation
Trust in the M12 serrated washer is built through extensive field use and validation. Case studies and field tests consistently demonstrate how these washers effectively reduce maintenance intervals and improve the safety of mechanical assemblies. In real-world applications, engineers and maintenance professionals report a notable decrease in re-tightening operations and increased confidence in joint reliability, attributing these benefits to the washers’ serrated design.
In conclusion, the M12 serrated washer is not merely a component; it is a vital element in the engineering assemblies that sustain industrial operations worldwide. Its design, rooted in decades of mechanical engineering expertise, its adherence to authoritative standards, and its validation through extensive field use, make it an irreplaceable asset in securing structural integrity. For industries where safety and reliability are paramount, investing in high-quality M12 serrated washers is more than a wise decision—it is an essential practice.