Flange nuts, particularly the M10 size, are a staple in various industries that require secure fastening solutions. With their distinctive design flaunting a wide flange at one end, these nuts deliver unmatched performance by distributing the load of the nut over a larger area, thus reducing the risk of damage to the fastened material and minimizing the bolt loosening due to vibrations.
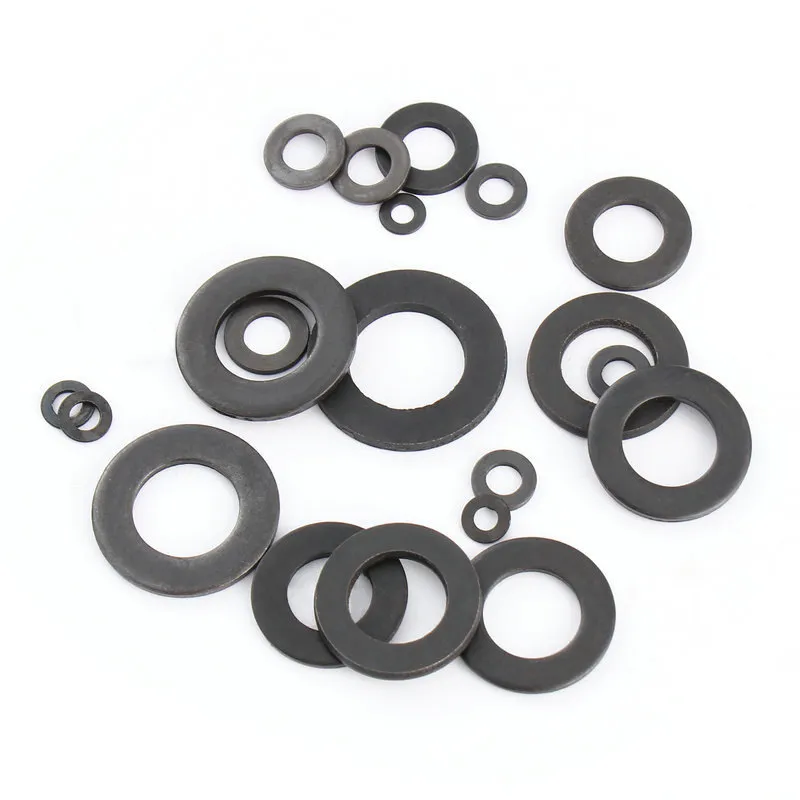
Drawing from extensive industry experience, flange nuts have shown to excel in scenarios where vibrations are a significant concern. For instance, in the automotive sector, where engine vibrations can lead to fastener loosening over time, M10 flange nuts offer a robust solution. The integrated washer-like flange not only eliminates the need for separate washers but also contributes to a more streamlined installation process. This added efficiency is invaluable in assembly lines where speed without compromising quality is essential.
From an expertise standpoint, selecting the right flange nut requires an understanding of both the application environment and the materials involved. The M10 flange nut, typically manufactured from materials like stainless steel or carbon steel, delivers resilience in corrosive environments, making them suitable for outdoor applications or high-moisture settings. In addition, the surface treatment of these nuts, whether it's zinc plating or black oxide coating, plays a crucial role in enhancing corrosion resistance and extending the fastener’s lifespan.
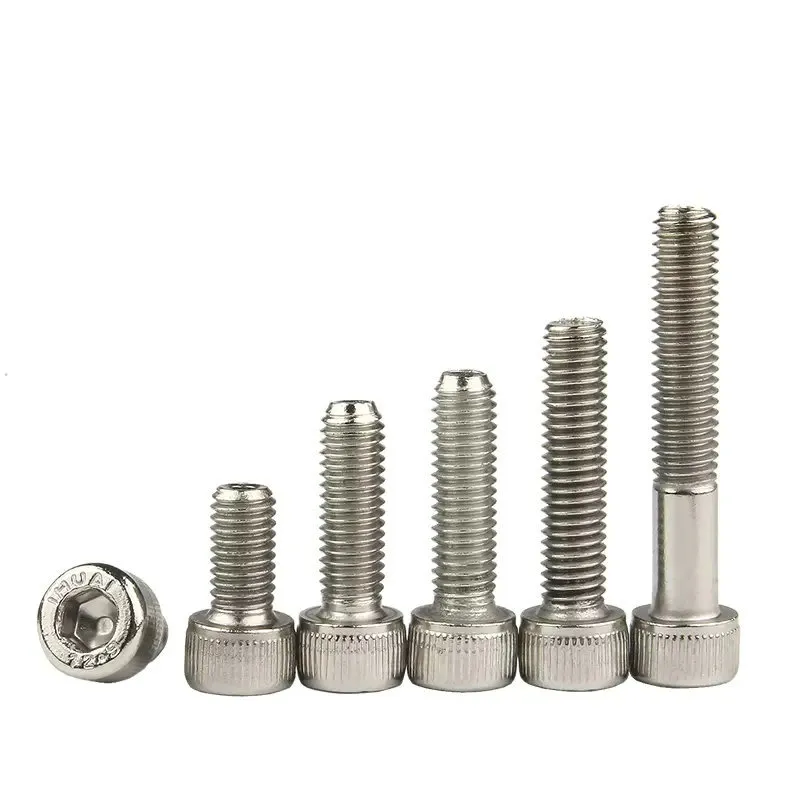
For industries requiring high precision and reliability, such as aerospace or heavy machinery, the mechanical properties of M10 flange nuts are worth noting. These nuts often adhere to rigorous national and international standards, ensuring they meet the required tensile and yield strengths. The M10 variety, specifically, is engineered to withstand significant mechanical stress, providing both peace of mind and operational reliability in critical applications.
flange nut m10
From the perspective of authoritativeness, numerous industry standards and certifications back the reliability of M10 flange nuts. Consider standards such as ISO and ASTM, which provide guidelines on material, dimensions, and mechanical properties, ensuring that these nuts are of the highest quality and can be used reliably across various applications globally. Manufacturers who adhere to these standards not only enhance the trust in their products but also assure clients of predictable performance under demanding conditions.
Trustworthiness in flange nuts, particularly the M10 type, is enhanced by advancements in manufacturing technologies. Modern digital manufacturing techniques allow for precision engineering and consistent quality control, ensuring each nut meets the expected specifications. Furthermore, companies that offer thorough traceability of their products, from raw material sourcing to final production, stand out in providing trustworthy solutions that assure end-users of both quality and ethical production practices.
Whether used in construction, manufacturing, or repair operations, the practical experience of integrating M10 flange nuts into projects reveals several benefits. Their ease of installation, combined with robust design, reduces installation errors, thus minimizing the potential for costly rework. Moreover, their ability to maintain joint integrity under dynamic conditions makes them indispensable in applications where safety and performance are paramount.
In conclusion, the M10 flange nut is more than just a fastener; it is a critical component engineered to withstand unique operational challenges. Through expert design, adherence to stringent standards, and a proven track record in diverse applications, M10 flange nuts exemplify engineering excellence and reliability. For industries looking to optimize their assemblies while ensuring safety and functionality, these nuts offer a trusted and authoritative solution.