Crafting the optimal fastener design requires a delicate balance between engineering precision and practical application. Over the years, advancements in material science and mechanical engineering have profoundly influenced fastener technology, offering us an array of solutions for numerous industries. Drawing from hands-on experience, let’s delve into the nuances that blend expertise and innovation to create superior fastener designs.
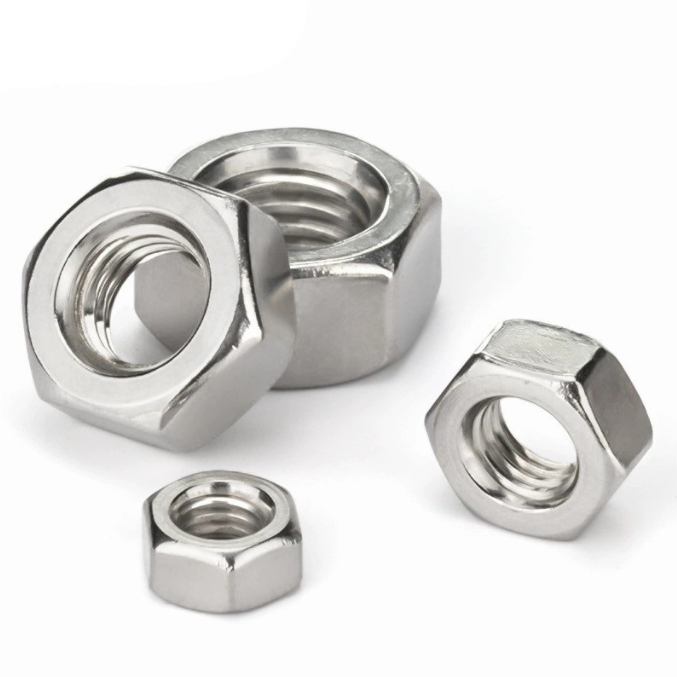
Fasteners, though often perceived as small components, play a pivotal role in securing the integrity of applications across sectors such as aerospace, automotive, construction, and electronics. Therefore, the design of fasteners must prioritize mechanical properties like tensile strength, shear resistance, and fatigue durability. For instance, in aerospace applications, where safety margins are minimal, titanium alloy fasteners are preferred due to their high strength-to-weight ratio and corrosion resistance.
One of the critical aspects of fastener design is understanding the operational environment. Fasteners must withstand various stresses and strains specific to their application domain. A frequently encountered issue is galvanic corrosion, particularly in maritime applications, where dissimilar metals in contact with an electrolyte can degrade over time. Designing fasteners that incorporate zinc coatings or sacrificial anodes can effectively mitigate this issue, enhancing their lifespan.
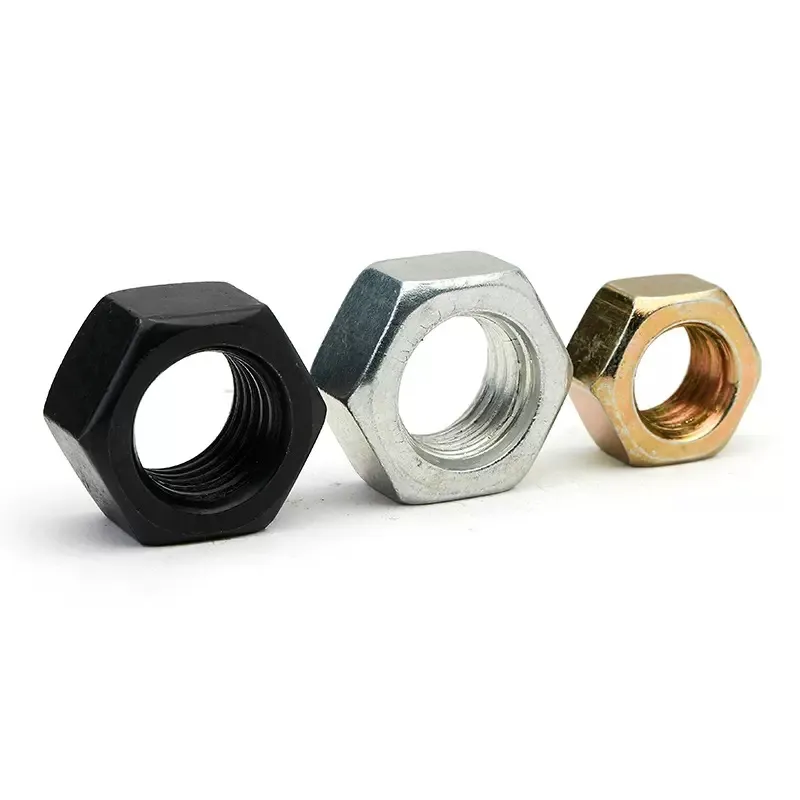
Expertise in fastener design also calls for a meticulous approach to thread geometry. The thread design impacts load distribution and the fastener’s ability to maintain joint integrity under dynamic conditions. Engineers experienced in fastener design often employ advanced software simulations to model stress and deformation, refining thread patterns to ensure uniform load distribution without compromising on ease of assembly.
One cannot overlook the importance of coatings and finishes in extending the life and performance of fasteners. Advanced coatings such as polytetrafluoroethylene (PTFE) and zinc-nickel offer notable enhancements in terms of reducing friction and increasing resistance to harsh environmental conditions. Such innovations reflect the growing trend towards materials that can adapt to a wide range of operational scenarios without losing functionality.
fastener design
Fastener design is an ever-evolving field that thrives on continuous research and development. Collaborations between industry leaders and research institutions foster breakthroughs that herald new standards. Patented designs, resulting from years of research, showcase the authoritative advancements in fastener technology. Companies like Hilti and Fastenal are renowned for their cutting-edge designs that not only meet existing needs but anticipate future demands.
A credible fastener design reflects a deep understanding of both the material science and the practical constraints imposed by real-world applications. Professionals in the field emphasize the relevance of thorough testing regimes—conducted under simulated conditions that closely mimic actual usage scenarios—thereby reinforcing trust in their designs.
Finally, the future of fastener design is poised on the brink of transformation with the advent of smart fasteners. By integrating sensors and IoT capabilities, these smart solutions can provide real-time data on stress, torque, and environmental conditions, moving fastener technology into a new era of proactive maintenance and enhanced safety.
In summary, fastener design is a discipline that blends engineering expertise, innovative materials, and real-world experiences to create solutions that are not only robust and reliable but also adaptable to the ever-changing demands of modern industry. As the field continues to evolve, it will undoubtedly set new benchmarks in precision, efficiency, and sustainability.