Precision flat washers are an essential component in many mechanical assemblies, providing a number of significant benefits that enhance the performance and longevity of various applications. Designed to provide a precise and consistent space or load distribution between components, these washers are crucial in industries ranging from aerospace to automotive to electronics.
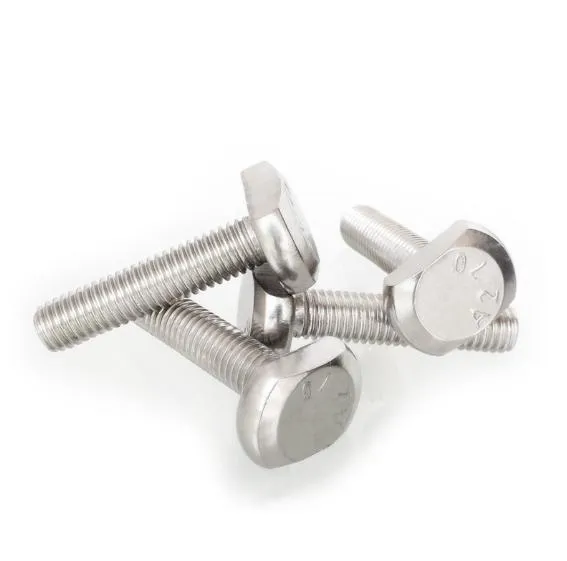
In the world of engineering and mechanics,
precision is not just a luxury—it's a necessity. The integrity of an assembly often depends on the accurate and reliable distribution of forces, which is where precision flat washers come into play. Unlike standard washers, precision flat washers are manufactured to strict tolerances, ensuring consistent thickness and flatness. This precise manufacturing means they can be relied upon to distribute loads evenly, maintain tension, and reduce the risk of loosening due to vibrations or thermal expansion.
One of the primary experiences shared by mechanical engineers is the challenge of dealing with uneven force distribution in assemblies. Without the use of precision flat washers, bolts and nuts can experience uneven stress, leading to premature failure or damage to the components. By incorporating precision flat washers, engineers can mitigate these risks, ensuring a longer lifespan for both the fasteners and the components they are designed to hold together.
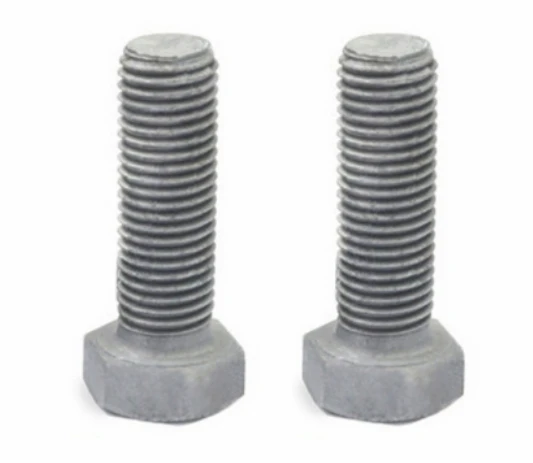
From a professional and expertise standpoint, choosing the right washer can often be as critical as selecting the proper bolt or screw. Precision flat washers are often recommended by experts in the field for applications where tolerance and consistent performance are paramount. These washers are typically fashioned from materials like stainless steel, brass, or specialized alloys, chosen for their resistance to corrosion and ability to withstand high loads.
precision flat washers
Moreover, the authority of using precision flat washers is further established through rigorous standards set by organizations such as the American National Standards Institute (ANSI) and the International Organization for Standardization (ISO). These standards ensure that precision washers meet specific levels of performance, providing engineers and end-users with the trust they require in their components. Compliance with these standards not only verifies quality but also assures end-users of the washer's reliability and effectiveness in their specific applications.
The trustworthiness of precision flat washers is paramount, especially in critical applications such as aerospace, where a single component failure can lead to catastrophic results. Manufacturers of precision washers often subject their products to stringent testing, including load distribution analysis, corrosion resistance under various environmental conditions, and thermal stability tests. This rigorous testing ensures that every washer performs under the highest standards, delivering reliable results every time.
When considering precision flat washers, it's also worth noting the advancements in manufacturing technologies that contribute to their quality. Modern computer numerical control (CNC) machining allows for the production of washers with exceptional precision, reducing variability and improving the fit and performance of each washer. This technological edge provides manufacturers with the ability to produce custom washers to meet specific application requirements without compromising on quality.
In conclusion, precision flat washers are more than just a simple component in an assembly. Their role is crucial in ensuring the longevity, reliability, and performance of mechanical assemblies across various industries. With a strong foundation in engineering expertise, authoritative standards, and proven trustworthiness, precision flat washers continue to be an indispensable element for achieving optimal results in mechanical design and maintenance.