Plain washers, particularly those conforming to the DIN 125 standard, hold a significant place in numerous mechanical applications. These seemingly simple components are engineered with precision to ensure optimal performance and reliability in various uses. As a professional in the field of mechanical design and manufacturing, appreciating the value of these washers goes beyond their basic function of distributing load.
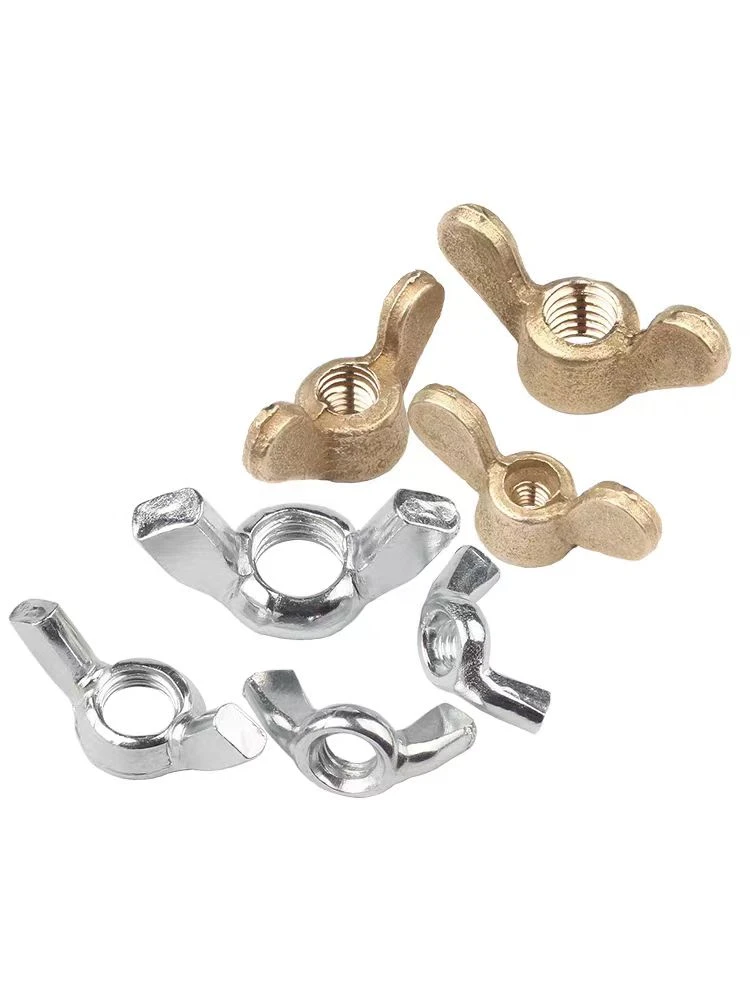
Understanding the dynamics of plain washers, especially the DIN 125 variety, is crucial for ensuring the longevity and efficiency of mechanical assemblies. These washers are essential in providing a smooth, stable surface for distributing the load of threaded fasteners, thereby preventing surface damage and ensuring an even distribution of load across the connected components. This load distribution is vital in maintaining structural integrity and preventing the loosening of nuts and bolts due to vibrations or dynamic loads.
Experts in mechanical engineering often emphasize the importance of adhering to standards like DIN 125, which guarantees that the washers conform to specific dimensions and material characteristics. By adhering to such standards, engineers ensure compatibility in assembly and uniform performance across different applications. DIN 125 plain washers are typically made from high-quality materials, such as stainless steel or carbon steel, each offering distinct benefits such as corrosion resistance or enhanced strength. Choosing the correct material based on the application environment is critical for achieving optimal performance.
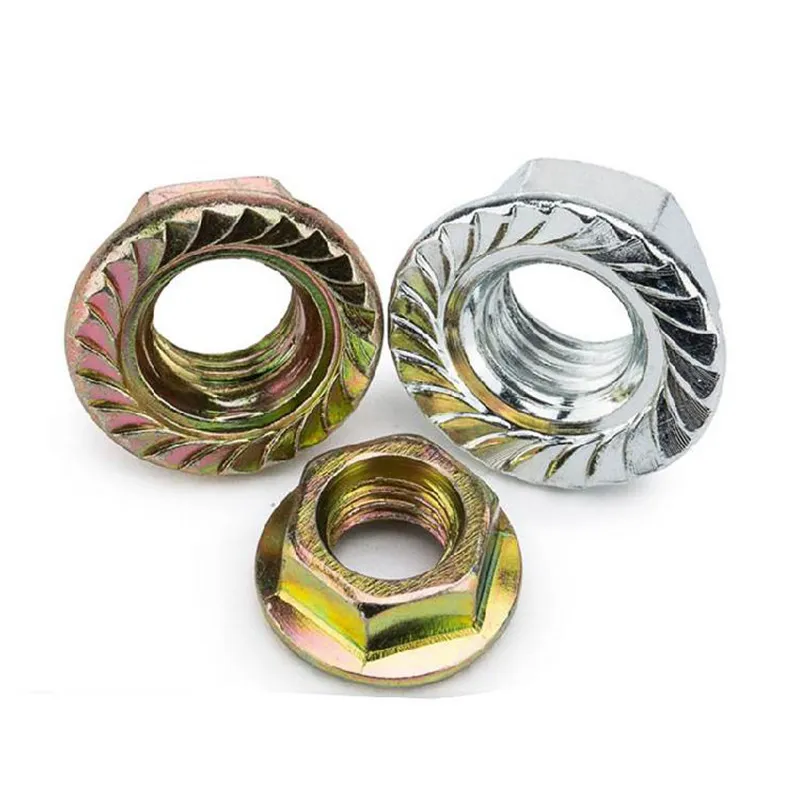
From a professional standpoint, using DIN 125 plain washers signifies a commitment to quality and precision in engineering projects. These components are essential in various industries, from automotive to construction, where reliability and durability are non-negotiable. Investing in standardized components like DIN 125 washers not only enhances the performance of the mechanical system but also significantly reduces the risk of component failure, which could lead to costly downtime or repairs.
plain washer din 125
Authority in this field is established through years of expertise and consistent delivery of high-quality results. Manufacturers and suppliers recognized for producing DIN 125 washers are often those that prioritize stringent quality control measures, ensuring each washer meets the specified dimensions and material standards. By sourcing washers from these reputable suppliers, professionals in the industry can ensure they are using components that meet the highest standards of safety and performance.
The trustworthiness of a product like the DIN 125 plain washer is built on its proven performance and reliability across countless applications. Professionals often share their experiences and insights into the effective use of these washers, emphasizing their role in reducing maintenance needs and enhancing the durability of mechanical connections. This peer validation builds trust in the product’s ability to deliver on its promises.
For industry professionals managing large-scale projects, the implementation of DIN 125 plain washers in designs is not just about following standards but also about integrating components that offer peace of mind. Knowing that the washers in use are designed to withstand specific mechanical stresses and are compliant with internationally recognized standards provides confidence in their long-term usability and safety.
In conclusion,
plain washers meeting the DIN 125 standard embody a combination of quality, precision, and reliability. Their role in ensuring the durability of mechanical connections cannot be understated. By prioritizing the use of these standardized washers, professionals demonstrate an unwavering commitment to quality and performance, setting a benchmark in the field of mechanical engineering. This dedication to excellence reinforces the trust and authority in the use of DIN 125 washers, making them an indispensable component in achieving engineering success across various industries.