Spring washers, often referred to as compression washers, play a critical role in various applications where maintaining tension is crucial. Crafted from high-grade materials, these mechanical components are indispensable in industries ranging from automotive to aerospace, ensuring operability and safety in equipment and structures.
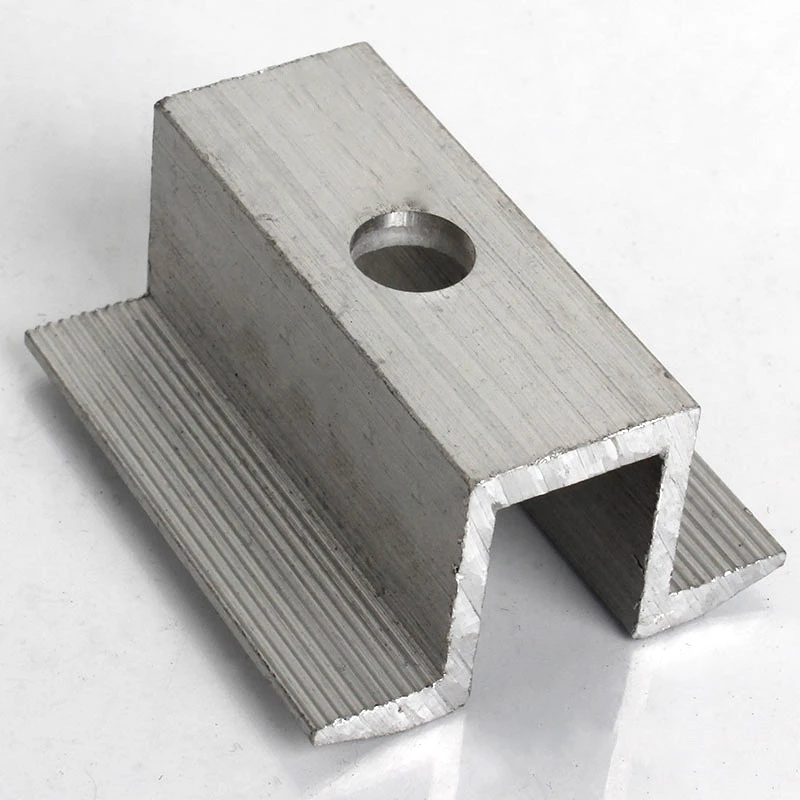
The inherent design of a spring washer distinguishes it from conventional flat washers. By featuring a slightly conical shape, spring washers are engineered to exert a continuous pressure on the fastener assembly. This attribute is particularly beneficial in dynamic settings where components are subject to vibration or thermal expansion, as the washer's compressive force prevents loosening and maintains joint integrity.
Professionals in fields demanding high levels of precision, such as engineering and manufacturing, appreciate the spring washer’s reliability. Its ability to absorb shock and distribute load evenly makes it a favored choice. For instance, in an automotive assembly, where parts constantly experience movement and stress, a spring washer acts as a buffer, safeguarding the fastened components from wear and tear while reducing noise and vibration.
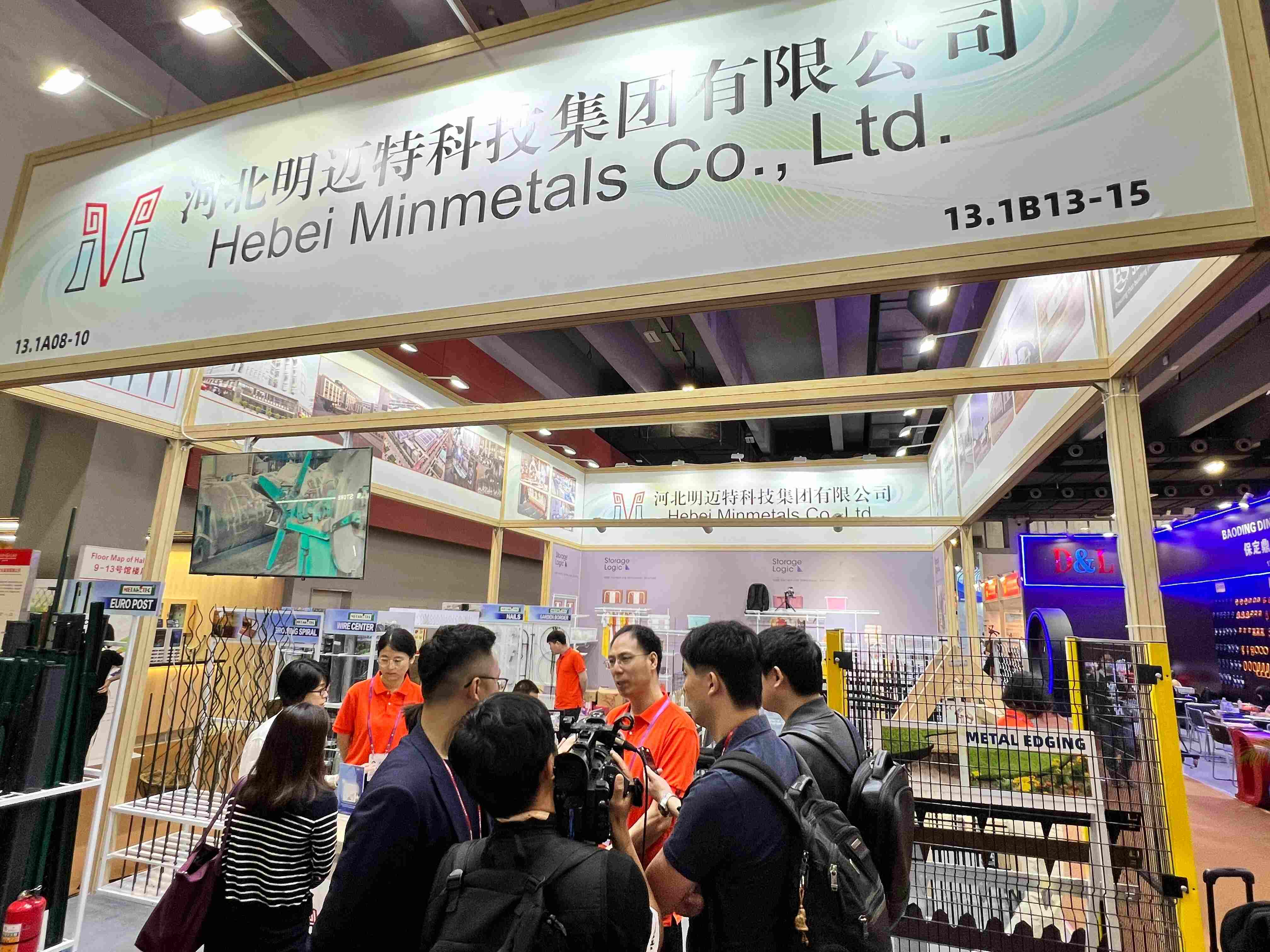
Further,
the versatility of spring washers cannot be overstated. They come in various materials, including stainless steel, phosphor bronze, and beryllium copper, each tailored for specific environmental conditions. Stainless steel spring washers are ideal for corrosion resistance in marine applications, whereas beryllium copper variants are excellent in electronic equipment for their electrical conductivity.
Despite their simple appearance, selecting the right spring washer requires a nuanced understanding of the application’s demands. Expert engineers assess factors such as load-bearing capacity, environmental conditions, and material compatibility before making a choice. This foundational expertise highlights the complexity behind these seemingly straightforward components.
spring washer compression
Moreover, the evolving landscape of technology continually impacts the development of spring washers. Innovations in material science have led to the creation of washers that can withstand higher pressures and extreme temperatures. This evolution ensures that spring washers meet the ever-increasing standards of modern engineering challenges.
Trustworthiness and performance are pillars of the spring washer manufacturing process. Leading manufacturers adhere to stringent industry standards, subjecting each batch of washers to rigorous testing. This commitment to quality control reflects the importance of reliability in mission-critical applications. Customers can rest assured that the spring washers they employ are not only designed with precision but have undergone comprehensive evaluation to ensure performance under pressure.
Establishing oneself as an authority in the field of spring washers involves staying abreast of industry trends and technological advancements. Engaging with communities, attending symposiums, and participating in collaborative research projects enhance the depth of understanding, fostering an environment where innovation in spring washer technology can thrive.
Personal experiences and case studies further establish credibility. For example, a project detailing the use of spring washers in a renewable energy installation not only demonstrates practical application but also highlights the strategic decision-making involved in ensuring operational efficiency and longevity of the system.
Spring washers, though often overlooked, are essential components that uphold the integrity of countless products and structures. By employing a combination of material expertise, engineering know-how, and commitment to quality, they continue to evolve, adapting to the complex and diverse needs of contemporary technology and industry. As these small yet mighty components continue to advance, their role in supporting innovation and safety across various sectors remains unwavering.