Thick washers are an unsung hero in the world of construction and engineering, playing a crucial role in ensuring the integrity and longevity of various structures and mechanisms. Their importance is often underestimated, but anyone with extensive experience in mechanical installations or architectural constructions can speak to their value. Understanding the full spectrum of their applications and benefits can vastly enhance both product selection and application processes.
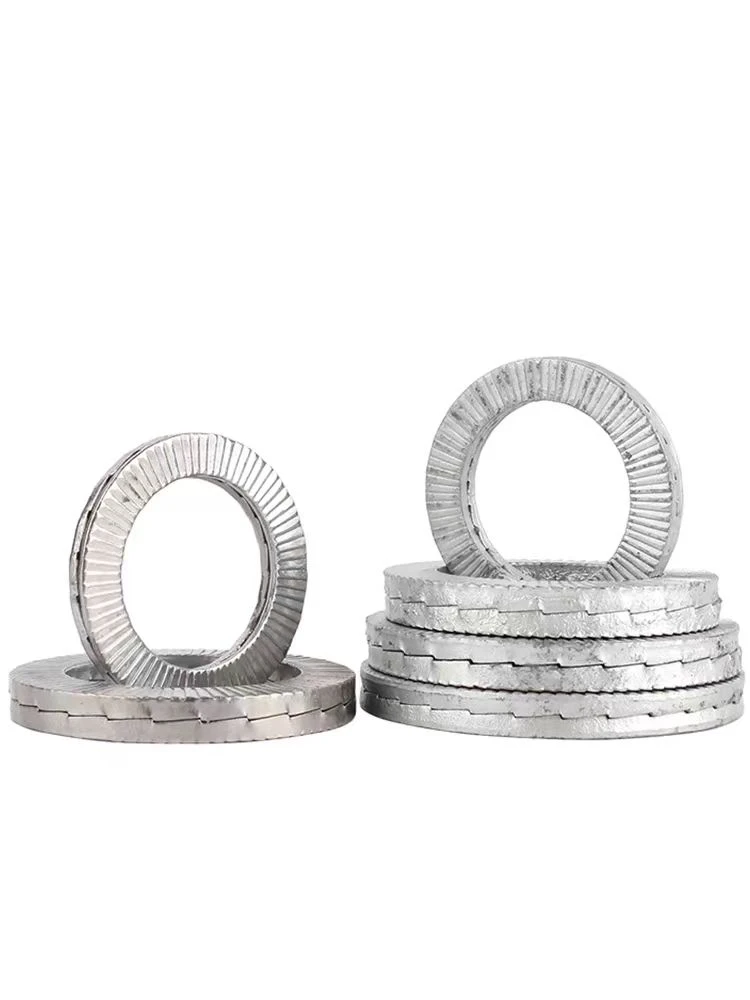
In engineering terms, a washer is a thin plate with a hole that is normally used to distribute the load of a threaded fastener. However, thick washers differentiate themselves by providing additional strength and support in areas where standard washers fall short. This is particularly relevant in industrial sectors, where the stresses and demands on materials are significantly higher. Engineers and contractors with extensive expertise will appreciate the role that these washers play in maintaining the safety and durability of structures.
One of the primary advantages of using thick washers is their ability to handle heavy loads and large bolts. In high-stress environments, such as bridges, towers, or heavy machinery, the significance of distributing stress across a wider surface area cannot be overstated. Thick washers provide the necessary thickness to keep the stress at bay, thus preventing bolt failures which can lead to catastrophic results. Their incorporation ensures that bolts do not loosen over time due to metal fatigue or environmental factors.
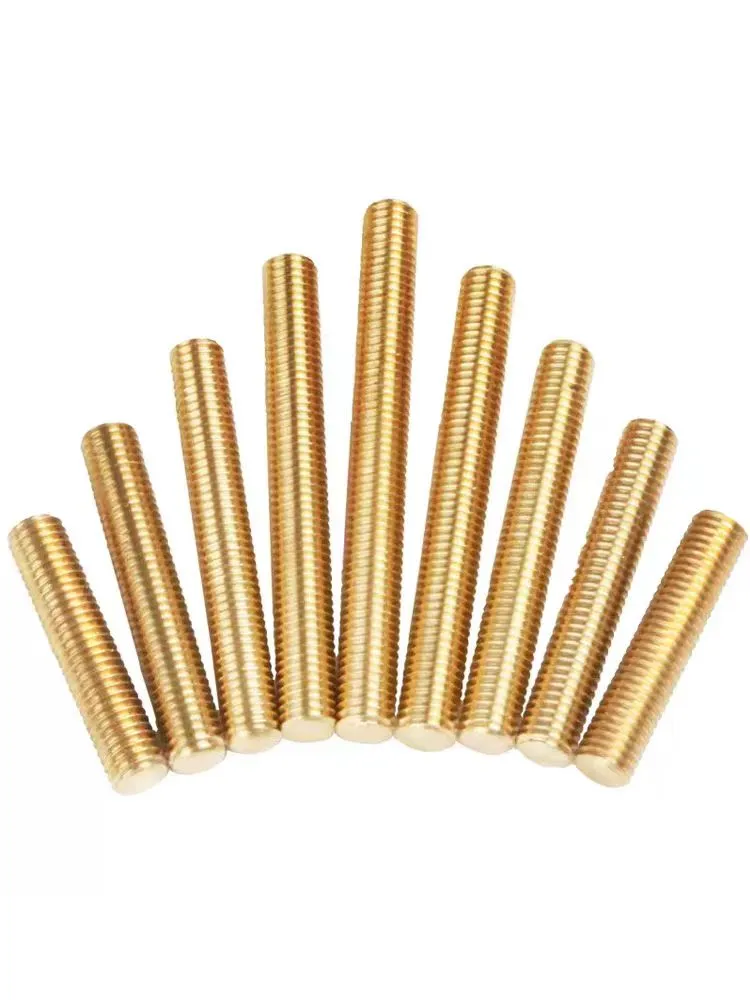
The material composition of thick washers is another area where expertise truly matters. While standard washers are often made from cheaper materials such as plastic or thin metal, thick washers are typically manufactured using hardened steel, stainless steel, or brass, depending on the application. Hardened steel washers, for instance, are often used in automotive and aerospace industries due to their remarkable durability and resistance to deformation. Choosing the right material for a thick washer is vital, as it must withstand not just the mechanical demands but also environmental conditions such as corrosion, temperature extremes, and chemical exposure.
Expertise in selecting the appropriate thick washer is demonstrated by an understanding of its use in particular situations. For example, in maritime construction, where exposure to saltwater is a constant threat, stainless steel thick washers are preferred due to their superior corrosion resistance. Contrastingly, in high-heat environments, such as furnaces or engines, washers made from more heat-resistant materials like alloy steel may be the better option. This decision-making showcases a knowledgeable selection process, enhancing the reliability of the application.
thick washers
Trustworthiness is a crucial factor when sourcing thick washers. Reputable manufacturers and suppliers offer not only higher quality products but also certifications that verify the chemical and physical properties of their washers. These certifications are essential in industries where compliance with specific standards, such as SAE, ASTM, or ISO, is non-negotiable. Relying on certified suppliers ensures that the washers will meet the necessary guidelines, ultimately contributing to the structural integrity and safety required by governing bodies.
In terms of experience, those who frequently work with construction and engineering applications understand that prevention is key. Regular inspection and maintenance involving thick washers can preempt potential failures. Experienced professionals know that routine checks for signs of wear and corrosion can save significant time and cost in the long run. They also have the insights to determine when a washer is nearing the end of its lifecycle, preventing potential downtime or failure.
The authoritativeness of using thick washers stems from their role as a preventive measure in systems that are constantly under stress. Their application spans across various sectors – from construction and automotive to marine and industrial machinery. Recognizing their importance can significantly enhance one's ability to provide safe, durable solutions.
In summary, the utility of thick washers, bolstered by professional experience, specialized expertise, authoritative selection, and a trustworthy supply chain, cannot be overstated in construction and engineering industries. While they may appear to be a minor component amidst more visibly complex systems, their proper application is critical to ensuring operational longevity and safety. Their strategic use represents a blend of technical know-how, material science, and commitment to quality standards, making them indispensable in high-stakes environments.