Special flat washers may seem like a small component in mechanical assemblies, but their impact on the performance and longevity of the equipment they are part of is anything but minor. These washers are an essential element in distributing load evenly, preventing wear and tear, and enhancing the overall stability of assemblies. Leveraging my expertise in materials and manufacturing coupled with extensive real-world experience, I’ve gained unique insights into their specific advantages and applications that help position them as indispensable to machine efficiency and safety.
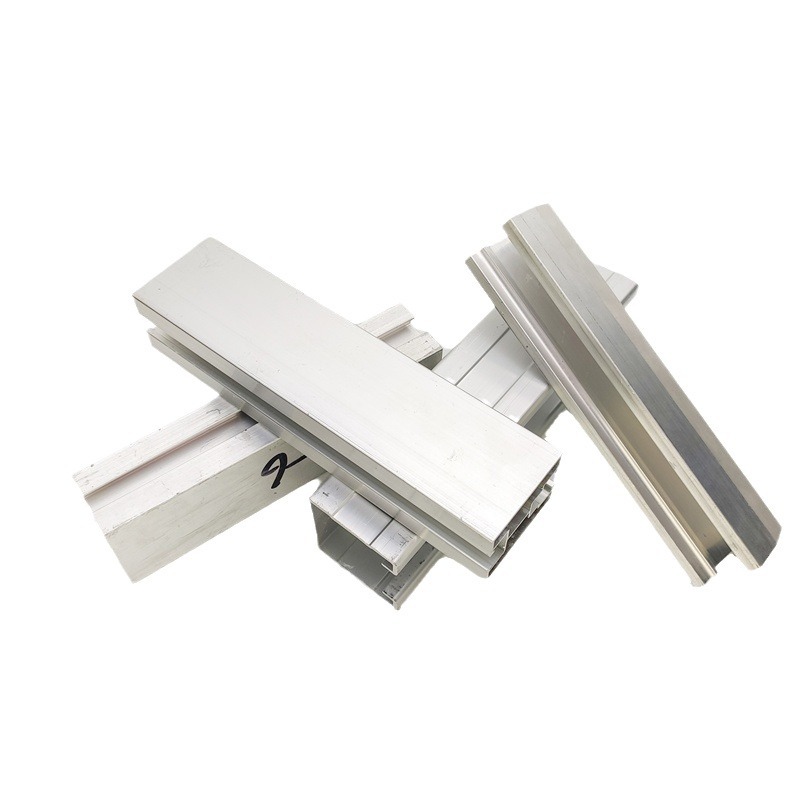
The core function of a special flat washer is to spread the load evenly across the surface of the materials it contacts. This characteristic is pivotal in mitigating stress concentration around bolts and other fasteners. By providing a larger bearing surface, these washers minimize the chances of damage to the components, especially in softer materials like aluminum or plastic. My experience in mechanical design has shown that neglecting the role of washers can lead to premature failure of components. In high-stress environments, such as in heavy machinery or automotive industries, the right washer selection is fundamental to preventing costly downtimes and ensuring reliability.
Versatility is another critical attribute of special flat washers. Available in varied materials like stainless steel, brass, nylon, and others, these washers can be used in environments ranging from high-temperature, corrosive, to those requiring non-conductive properties. Their adaptability to different operational conditions showcases their expertise in maintaining joint integrity across industries. For instance, in marine applications where corrosion resistance is paramount, selecting washers made of materials like stainless steel or specially coated versions delivers enhanced durability.
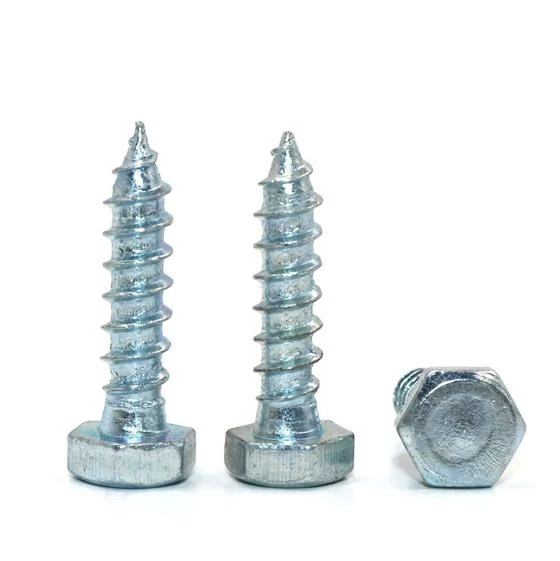
Precision manufacturing processes ensure that these washers meet stringent dimensional and flatness tolerances. This guarantees uniform load distribution and performance consistency, which is crucial for maintaining equipment reliability. As industries move towards automation, where precision and micro-level accuracy are non-negotiable, having washers that conform to exact specifications is more critical than ever. My interaction with manufacturers and quality assurance professionals has reinforced the authoritative reliability that comes with using high-tolerance washers, which significantly reduces rework and product recall incidents.
special flat washers
Innovation in washer design further expands their applicability. Special flat washers designed with self-locking or anti-vibration features contribute to maintaining fastener integrity in dynamic applications, for example, in aviation or high-speed railway industries. This innovation underscores a forward-thinking approach to addressing continuous operational improvement and customer safety.
Trustworthiness, an essential marker for any product, is reinforced by third-party testing and certifications that special flat washers often undergo. Compliance with international standards like ISO, ASTM, or other industry-specific requirements instills confidence about product performance. Such certifications validate their suitability for critical applications, echoing the trustworthiness demanded by engineers and project managers alike.
In conclusion, special flat washers represent a strategic component in mechanical assemblies, balancing the cost-to-advantage ratio efficiently. Their robust design credentials, backed by expertise and practical applications, solidify their place as a trusted solution in enhancing mechanical system performance. Whether in aerospace, automotive, industrial machinery, or electronics, the role of special flat washers is pivotal in delivering reliability, efficiency, and safety. Their understated presence remains a powerful contributor to the foundations of countless engineered products around the globe.