Sheet metal fasteners are pivotal components widely used in various industrial and commercial applications, enhancing the structural integrity and functionality of metal assemblies. In an era where precision engineering and reliability are paramount, understanding the variety and applications of these fasteners is crucial for manufacturers, engineers, and end-users alike.
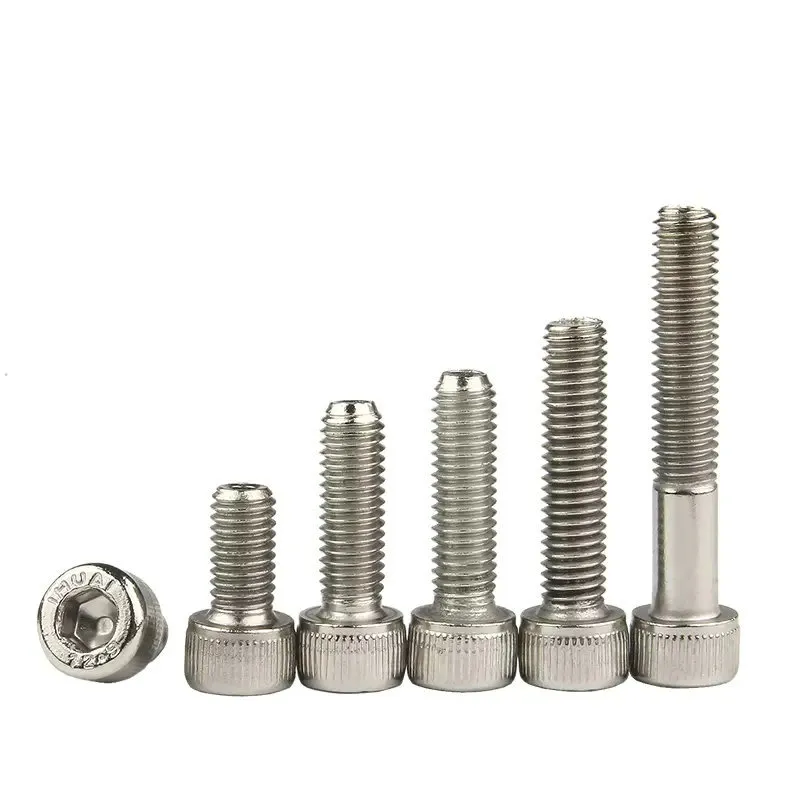
Sheet metal fasteners come in a diverse range of types, each meticulously designed to fulfill specific requirements. Some of the most common include self-clinching nuts and studs, threaded inserts, rivets, and captive screws. Self-clinching fasteners are renowned for their high-performance integration into sheet metal work. These fasteners, coined for their ability to fasten within metal sheets through cold flow, offer seamless installation and impressive resistance to vibration while maintaining the host material's strength.
The innovation in fastener technology hasn't just stopped at design; materials play a pivotal role too. Modern sheet metal fasteners are crafted from stainless steel, brass, aluminum, and even high-strength alloys to cater to niche applications requiring diverse properties like corrosion resistance, conductivity, or weight reduction. This variety ensures that solutions are available for use in harsh environments, including automotive, aerospace, marine, and electronics industries.
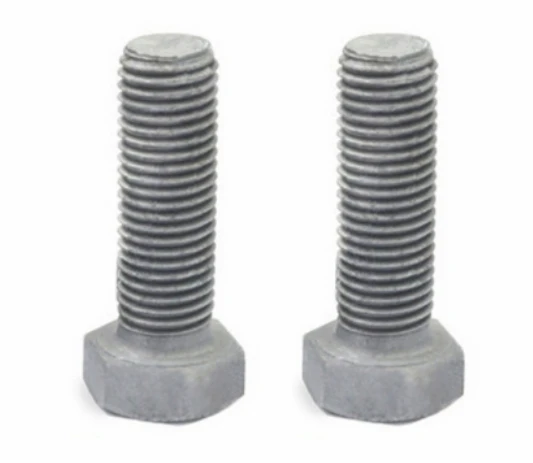
Product selection should always align with project requirements. Engineers must consider factors like tensile strength, locking mechanism, corrosion potential, and the environment in which the fastener will operate. For example, electronic assemblies benefit from using non-magnetic or non-conductive fasteners to minimize interference, whereas aerospace components might require high-strength, lightweight fasteners to optimize performance and efficiency.
Manufacturers of sheet metal fasteners continuously innovate to provide enhanced solutions. The introduction of automated installation systems has revolutionized productivity and precision, reducing manual errors and installation time. This automation integrates well into the modern production lines that prioritize speed while maintaining high standards of quality assurance.
sheet metal fasteners
Another critical aspect is the sustainability of these components. With increasing emphasis on green manufacturing, fastener production now often involves eco-friendly processes. Furthermore, some fasteners can be designed for easy disassembly, facilitating recyclability which aligns with the circular economy principles.
End-users and project managers should prioritize suppliers that demonstrate expertise and reliability. A trusted supplier not only provides high-quality fasteners but also offers services such as technical support, material certification, and compliance with industry standards which are indispensable for ensuring that the fasteners meet rigorous application demands.
The expertise of industry leaders and engineers shines brightest when addressing challenging applications. The right fastener selection is no mere afterthought; it represents an intersection of experience, authority, and trust in ensuring the safety, functionality, and durability of metal assemblies.
Engineers should leverage a combination of empirical testing and historical data to validate their fastener choices.
In conclusion, sheet metal fasteners, though small, play a colossal role in the functionality, durability, and safety of metal structures. Their continued evolution in terms of design, material, and application signifies an ongoing quest for excellence within the industry. Choosing the right fasteners involves tapping into a reservoir of expertise, recognizing the authority of innovators, and establishing a foundation of trust with reliable suppliers to ensure optimal performance in any application.