The M7 spring washer, often overlooked in the realm of mechanical components, plays a crucial role in ensuring the integrity and longevity of assemblies. Its unique design and function make it indispensable in a wide array of applications, from automotive assemblies to high-level engineering projects. Understanding its uses, benefits, and material properties can significantly enhance the decision-making process for engineers and procurement specialists.
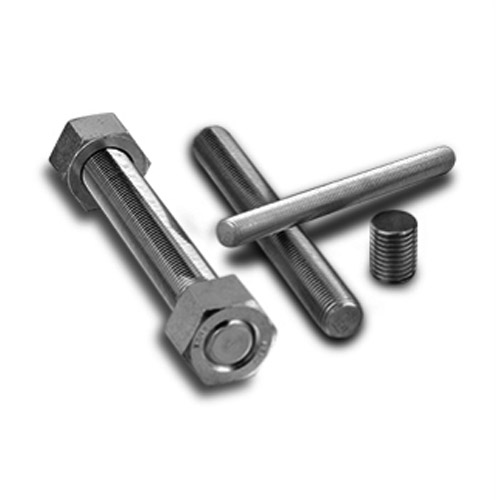
Spring washers, particularly the M7 size, are renowned for their ability to maintain tension in assemblies that are subject to vibration, thermal expansion, and differential wear.
The M7 spring washer is specifically engineered to accommodate various shaft sizes effectively. With an outside diameter typically ranging around 14mm and an inner diameter that suits an M7 bolt, it prevents loosening by exerting a frictional force and maintaining a preload between the bolt head or nut and the substrate it fastens.
This washer is most commonly fabricated from high-quality spring steel. This material choice is not arbitrary; it capitalizes on steel's inherent properties like hardness and its excellent fatigue resistance. Furthermore, proprietary surface treatments, such as zinc plating or black oxide finish, enhance their corrosion resistance, making them suitable for harsh environments. The choice of material is crucial because it determines the washer's mechanical properties, including tensile strength and resistance to deformation under load.
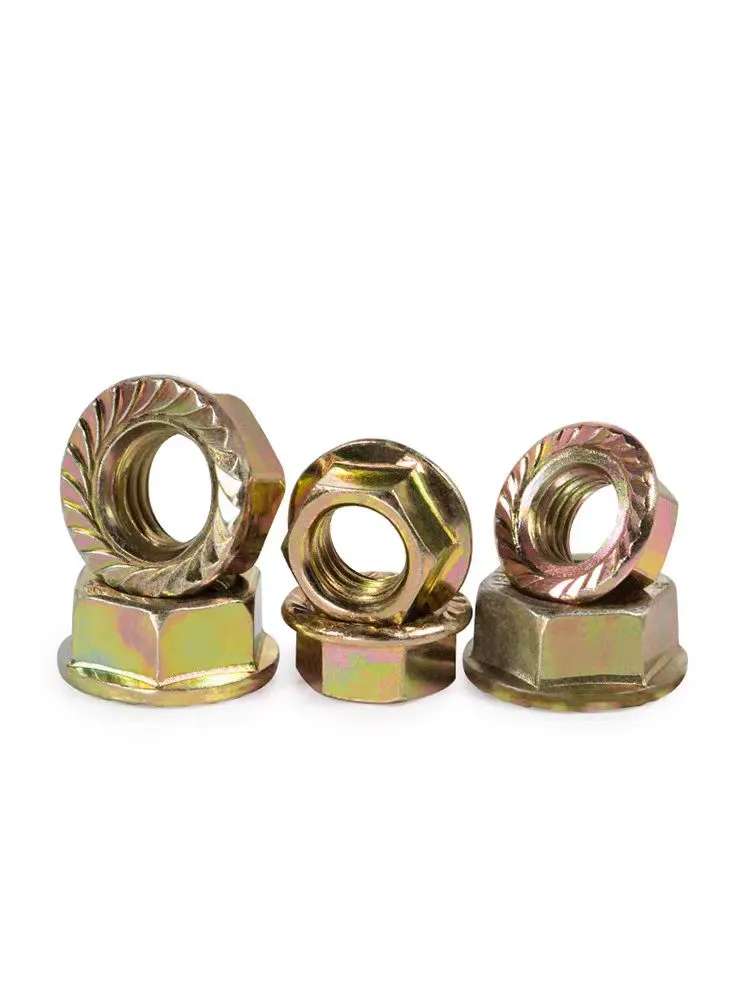
In practical application, the M7 spring washer serves a vital function by absorbing initial shock loads and ensuring tension is distributed evenly across the surface area it contacts. This is critical because uneven tension can lead to premature bolt failure or the disintegration of the joint, resulting in costly downtimes or catastrophic failures. These washers are particularly advantageous in automotive applications, where vehicles are often subjected to intense vibrations and temperature variances. By using M7 spring washers, automotive manufacturers enhance the safety and reliability of their products.
m7 spring washer
The technical expertise necessary to select the appropriate spring washer involves a detailed analysis of the joint conditions and load requirements. Engineers must consider factors such as the washer's load distribution, elasticity, and the environment in which the assembly will operate. Knowledge in metallurgical properties of the materials used in conjunction with these washers is essential for making informed decisions to prevent corrosion-related failures and mechanical fatigue.
The M7 spring washer is not only a component of high mechanical utility but also one of strategic economic significance. By preventing assembly disintegration, these washers reduce maintenance costs and extend the lifespan of machinery and components they are integrated into, leading to a more sustainable operation. Their reliability fosters trust among engineers and project managers who depend on consistent performance for safety-critical applications.
Understanding the benefits of the M7 spring washer through personal experience provides a solid foundation for recommendation in professional settings. Engineers who've implemented these washers report a noticeable decrease in maintenance interventions and improved system reliability. In sectors where safety cannot be compromised, such as aerospace and automotive, reliance on such components underlines their authority and trustworthiness in maintaining system integrity.
In the global market, where competition for product differentiation is fierce, leveraging the M7 spring washer as part of a robust design process can provide a competitive edge. Trust in the use of M7 spring washers is built on a track record of performance and expertise in product selection and application, making them a staple in the toolkit of engineers aiming for excellence in mechanical design and production.