The Significance and Application of Headed Weld Studs
Headed Weld Studs, also known as Weld Nuts or Threaded Weld Studs, are an essential component in various industrial applications where strong, durable connections are paramount. These studs, with a head on one end and a threaded shaft on the other, offer a versatile solution for welding and fastening tasks, particularly in situations where accessibility is limited or where high-strength joints are required.
The headed part of the stud refers to its flat or domed head, which not only provides a stable platform for welding but also adds an extra layer of security to the joint. The head distributes the load evenly, preventing stress concentration and reducing the risk of failure. On the other end, the threaded section allows for easy mating with nuts and bolts, providing a secure, thread-to-thread connection.
Weld studs find their utility in a wide range of industries, including automotive, aerospace, construction, and manufacturing. In the automotive industry, they are used for chassis assembly, body panel attachment, and engine mounting, ensuring robust connections that can withstand extreme conditions. In aerospace, headed weld studs provide reliable connections in aircraft structures, where lightweight yet strong materials are crucial.
The process of using headed weld studs involves a technique called 'welding.' The stud is first positioned onto the workpiece and then fused to it through a welding process such as arc welding, resistance welding, or even laser welding. This method offers a permanent, high-strength bond that can withstand significant mechanical stress and environmental factors This method offers a permanent, high-strength bond that can withstand significant mechanical stress and environmental factors
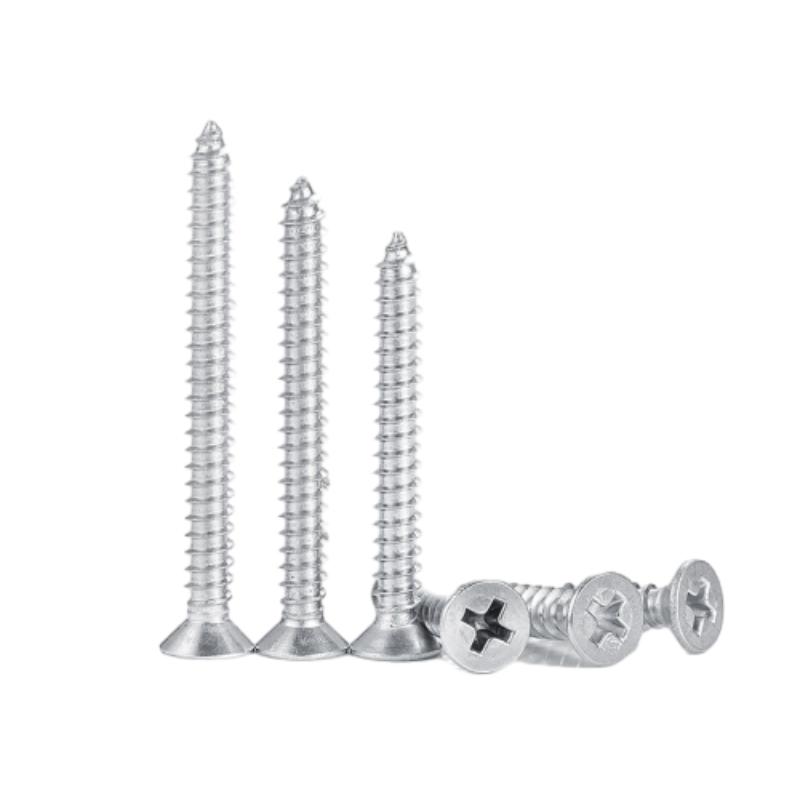
This method offers a permanent, high-strength bond that can withstand significant mechanical stress and environmental factors This method offers a permanent, high-strength bond that can withstand significant mechanical stress and environmental factors
headed weld studs.
One of the key advantages of headed weld studs is their ability to be pre-positioned before welding. This is particularly beneficial in situations where access is restricted or where precision is vital. Moreover, they can be installed at any angle, making them suitable for complex geometries and irregular surfaces.
Furthermore, headed weld studs reduce the need for additional drilling or tapping processes, saving time and cost in production. They also minimize the risk of thread damage, ensuring consistent quality and reliability in the final product.
In conclusion, headed weld studs are a critical element in modern engineering and manufacturing. Their design, combined with the welding process, offers a robust, efficient, and cost-effective solution for creating strong, long-lasting connections. As technology advances, headed weld studs will continue to play a pivotal role in industries that demand high-strength, precision-engineered joints.