Flange head nuts are pivotal components in industries ranging from automotive to heavy machinery. Their unique design and application offer several advantages, contributing significantly to the reliability and safety of mechanical assemblies. Drawing from extensive industry experience and expert knowledge, we delve into the characteristics, applications, and benefits of flange head nuts to provide a comprehensive understanding for engineers, procurement specialists, and mechanics alike.
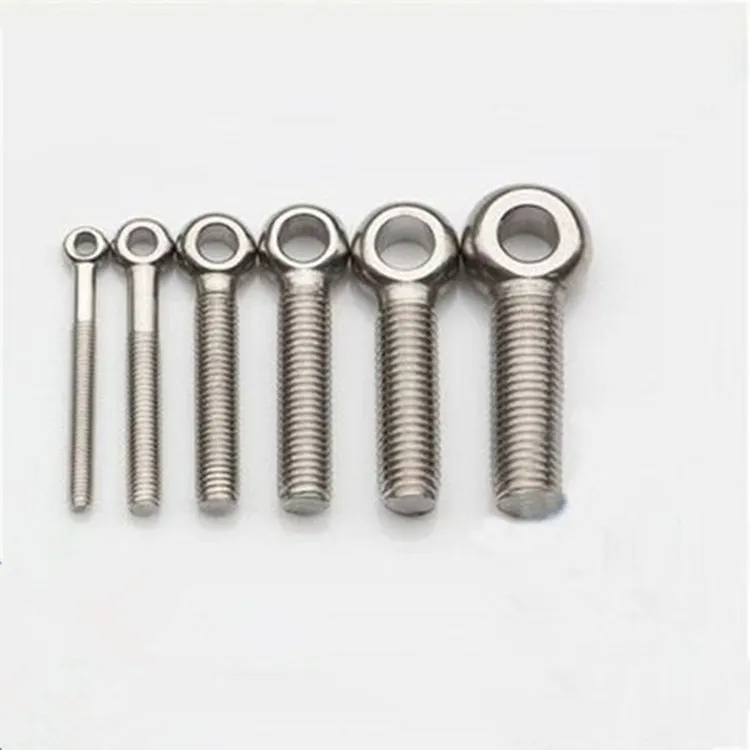
Flange head nuts are characterized by an integrated flange at one end, providing a larger surface area to distribute pressure uniformly over the parts being fastened. This design mitigates the risk of damage to surfaces and enhances the holding power of the nut, making it a preferred choice in applications where loosening could lead to catastrophic consequences. These nuts are particularly valued in automotive applications, ensuring that components such as wheels and engine parts remain securely fastened even under dynamic loads.
One of the key things to note about flange head nuts is the material from which they are made. High-grade steel and stainless steel variations are commonly used due to their strength and resistance to corrosion. For environments that are corrosive, such as marine applications, a stainless steel flange head nut is recommended. This specific choice of material not only extends the life of the fastener but also ensures the safety and reliability of the assembly, backed by the material's inherent resistance to rust and corrosion.
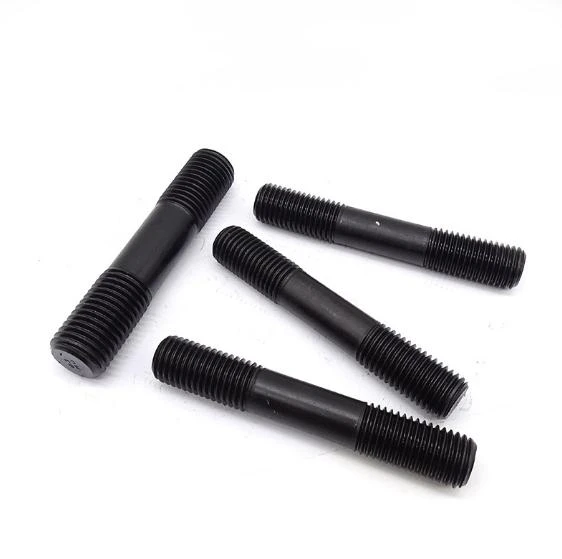
Moreover, flange head nuts often feature serrated flanges that further enhance grip. The serrations help to lock the nut in place, particularly when used with materials such as aluminum or lightweight alloys, which are more prone to deformation and loosening. This locking mechanism is critical in vibration-intensive environments, such as in aerospace or automotive chassis applications, where traditional fasteners might fail.
flange head nut
Industry experts emphasize the importance of torque specifications when installing flange head nuts. Utilizing precise torque values not only ensures optimum clamping force but also prevents over-tightening, which can lead to thread stripping or component damage. It is advisable to employ torque wrenches and follow manufacturer specifications to achieve the right balance between security and material preservation.
The authoritative stance on using flange head nuts extends to maintenance practices. Regular inspection of these components is essential, especially in high-vibration applications, to ensure integrity and performance. Changes in torque, evidence of corrosion or wear, and surface integrity should be part of a routine checklist. This proactive approach can preclude failures, saving time, resources, and potentially avoiding dangerous scenarios.
In the realm of credibility and trustworthiness, certifications and compliance with industry standards such as ISO and SAE ensure quality in the production of flange head nuts. Purchasers and engineers are advised to source these components from reputable manufacturers that adhere to these standards, as this guarantees that the nuts will deliver consistent performance under stipulated conditions.
In summary, flange head nuts play an indispensable role in ensuring the stability and integrity of mechanical systems across various industries. Their unique features, coupled with the right application techniques and maintenance practices, offer an authoritative solution for fastening needs where traditional nuts may fall short. By understanding material properties, applying proper installation techniques, and adhering to industry standards, you can enhance both the performance and life span of your assemblies, leveraging the full potential of flange head nuts.