The Art of Self-Tapping Screws Through Steel
Self-tapping screws are a marvel of engineering, designed to create their own thread as they are driven into materials. When it comes to working with steel, these screws become even more impressive due to the inherent strength and density of the metal. Tapping into steel requires precision, the right tools, and an understanding of the properties of both the screw and the material.
The process begins with selecting the appropriate self-tapping screw for the job at hand. Stainless steel self-tapping screws are highly recommended for use in steel applications because they possess similar physical properties, reducing the risk of thread stripping or screw failure. Titanium coating is another excellent option as it provides superior corrosion resistance and can significantly increase the screw's durability during installation.
Before driving the self-tapping screw into the steel, it is crucial to drill a pilot hole. This initial step is not merely a precaution but a necessity. The pilot hole diameter should be carefully chosen to match the core size of the screw, allowing smooth cutting of threads without cracking the steel or distorting the new threads. A drill bit suited for steel, often cobalt or high-speed steel (HSS), should be used for this purpose to ensure clean, precise holes.
Once the pilot hole is prepared, inserting the self-tapping screw requires steady pressure and the correct technique. Using a screwgun or a drill with a torque control setting helps manage the force applied, preventing over-tightening which could strip the threads or damage the steel surrounding the hole. As the screw is turned, its specially formed thread cuts into the steel, creating a tight fitting that is both secure and resistant to vibration As the screw is turned, its specially formed thread cuts into the steel, creating a tight fitting that is both secure and resistant to vibration
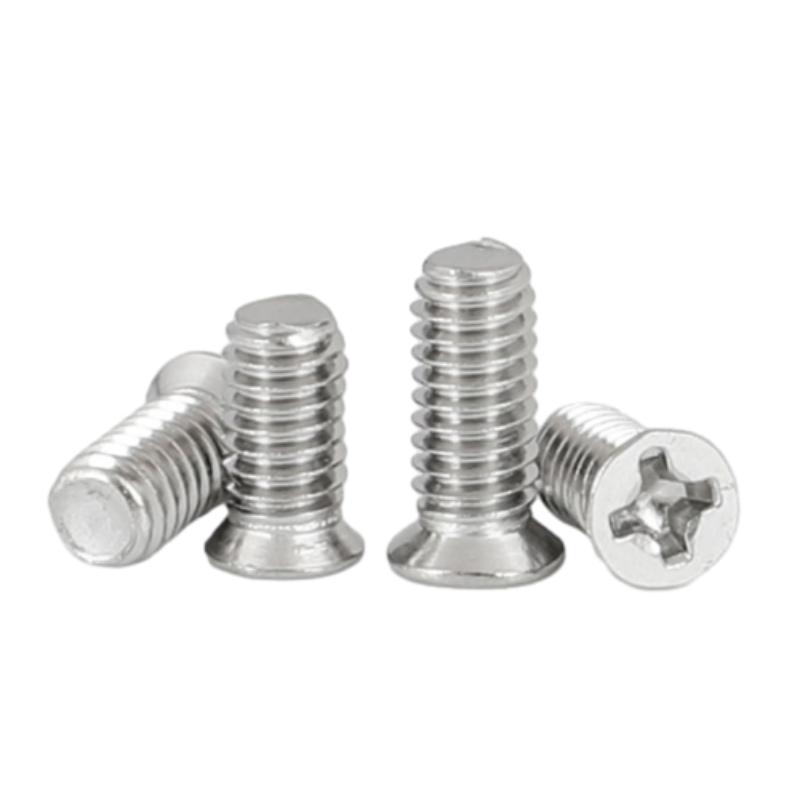
As the screw is turned, its specially formed thread cuts into the steel, creating a tight fitting that is both secure and resistant to vibration As the screw is turned, its specially formed thread cuts into the steel, creating a tight fitting that is both secure and resistant to vibration
self tapping screws through steel.
In applications where the steel is thicker or where greater structural integrity is needed, it may be necessary to use a tap to cut the threads before installing the screw. This two-step process ensures that the threads are precise and reduces the risk of cross-threading. However, with the advancements in self-tapping screw technology, direct insertion is often sufficient and preferred for speed and efficiency.
Throughout the process, lubrication can be advantageous in reducing friction and wear between the screw and the steel. Lubricants such as oil or wax can prolong the lifespan of both the tooling equipment and the screws themselves, while also making the insertion process smoother.
Using self-tapping screws through steel is an efficient method of fastening that saves time compared to traditional threading methods. It combines the steps of drilling and tapping into one, streamlining assembly processes. In industries ranging from automotive to construction, where robust connections are required, self-tapping screws provide a reliable solution that stands up to the demands of steelwork.
As with any fastener, however, it is essential to follow manufacturer guidelines for load specifications and application advice. Properly installed, self-tapping screws can provide a lifetime of service, securely holding together the intricate frameworks and structures that rely on steel's enduring strength.